Material testing is a crucial process in many industries to ensure the safety, quality and durability of materials. Precise and reliable monitoring of the gases produced is essential, particularly in the context of burning material tests, which assess the flammability of materials.
In addition, the NDIR sensors and smartGAS analyzers are robust and durable, making them ideal for use in demanding test environments. These features make them indispensable tools that not only significantly improve the accuracy of material testing, but also optimize the efficiency of testing processes. With continuous data transmission at a frequency of 10 Hz and a linearity error of less than 2 ppm, the analyzers contribute to seamless monitoring, leading to reliable results. In modern materials testing, such technological advances mean a significant increase in safety and sustainability - a requirement that is becoming increasingly important in the industry.
Basics of the Burning Material Test
Material testing is an essential part of ensuring the quality and safety of materials, especially when it comes to assessing flammability and the behavior of materials under extreme conditions. In safety-critical industries such as construction, automotive production and aviation, accurate testing procedures are essential to ensure compliance with high safety standards. The Burning Material Test is of particular importance here, as it shows how materials react to heat and flammability.
In this context, NDIR sensors and smartGAS analyzers play a crucial role as they enable precise and reliable gas measurement. NDIR sensor technology (non-dispersive infrared sensors) detects specific gases such as CO₂, CO and hydrocarbons that are released during the combustion process. Thanks to this high precision, the sensors are able to detect even the smallest concentrations of these gases. This is particularly important in order to be able to make exact statements about the flammability and safety of a material. The ability to react quickly - with a T90 time of less than 4 seconds - enables precise monitoring of emissions in safety-critical test situations.
The smartGAS analyzers also offer additional advantages that make material testing even more efficient. They are extremely precise and have a linearity error of less than 2 ppm, resulting in a very accurate gas analysis. Continuous data transmission at 10 Hz ensures that the entire combustion process can be monitored in real time. This continuous measurement means that even the smallest changes in the gas composition can be detected and evaluated immediately. This optimizes the safety and accuracy of these material tests.
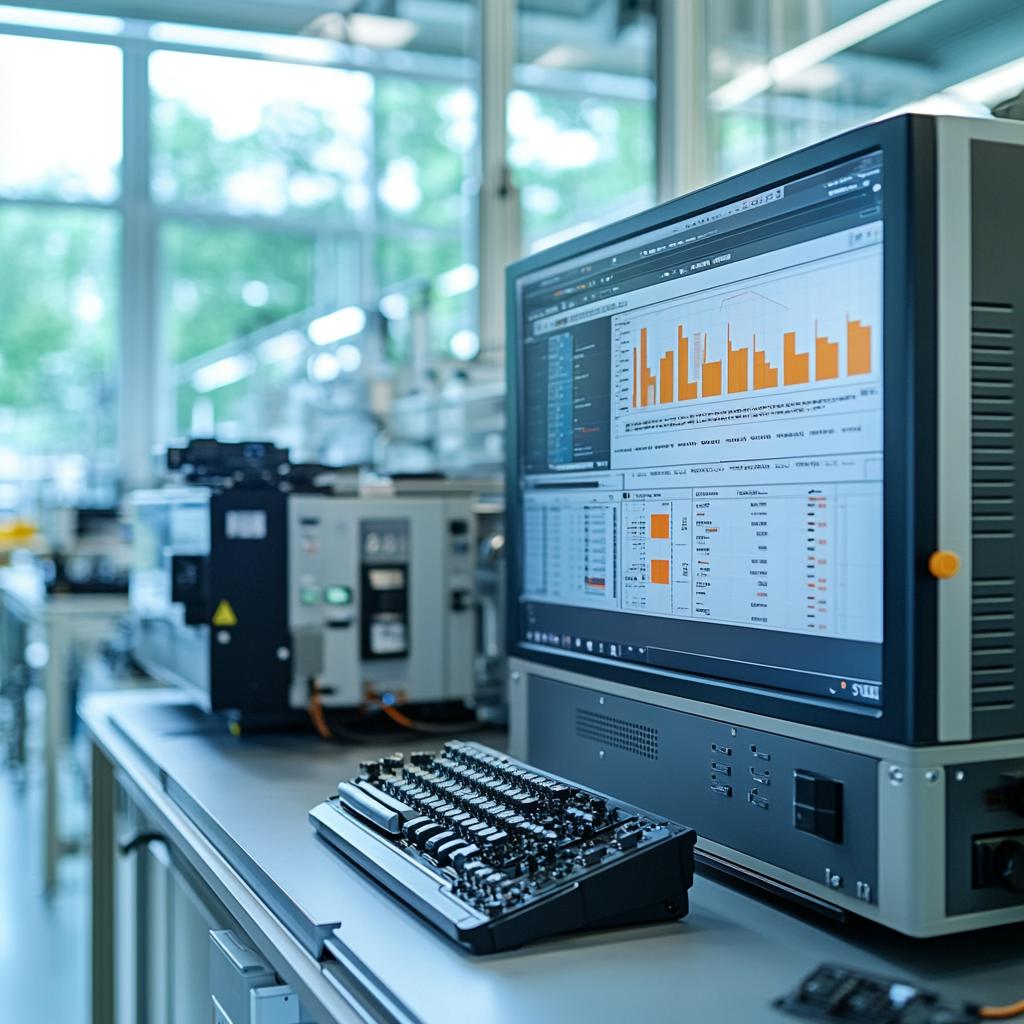
NDIR sensors and smartGAS analyzers are designed to work reliably in demanding environments. Whether in high-temperature areas or under extreme physical stress, these systems ensure consistently high performance and thus contribute to increased reliability in material testing.
By providing precise and fast measurements, NDIR sensors and smartGAS analyzers play a key role in ensuring that materials can be tested safely and in accordance with the prescribed standards. Companies that rely on these technologies therefore benefit from more efficient and accurate material testing, increasing safety and reducing long-term costs through fewer material failures. The combination of these technologies makes it possible to meet the growing demands for safety and precision.
Functionality of NDIR sensors in materials testing
The functionality of NDIR sensors (non-dispersive infrared sensors) is based on a precise physical principle that utilizes the absorption of infrared radiation (IR) by specific gas molecules. At the heart of this technology is the property of gases to absorb certain wavelengths of light when penetrated by infrared rays. Each gas has a specific absorption spectrum that is determined by its molecular structure. In NDIR technology, this effect is used to reliably detect gases such as carbon dioxide (CO₂), carbon monoxide (CO) and hydrocarbons.
Functionality in detail:
Infrared radiation source:
The NDIR sensor has an infrared radiation source that continuously emits IR light. This source can consist of a light bulb or an LED that is set to a specific bandwidth of infrared rays. This IR light is passed through the gas sample volume located inside the sensor chamber.
Gas sample and light absorption:
When the IR light hits the gas sample, it is partly transmitted through the gas and partly absorbed by the molecules of the gas. Each gas absorbs specific wavelengths of infrared light based on its molecular structure. For example, carbon dioxide (CO₂) typically absorbs infrared light at a wavelength of around 4.26 µm, while carbon monoxide (CO) absorbs at around 4.67 µm.
Filter and detector:
After passing through the gas, the remaining IR light reaches an optical filter that only allows the wavelength of IR light specific to the respective gas to pass through. This filter is tuned to allow only the wavelengths that absorb the gas to pass through. The detector, which is located behind the filter, measures the intensity of the IR light that passes through. The amount of light absorbed is directly related to the concentration of the gas in the sample - the higher the amount of gas, the more infrared radiation is absorbed and the lower the amount of light that reaches the detector.
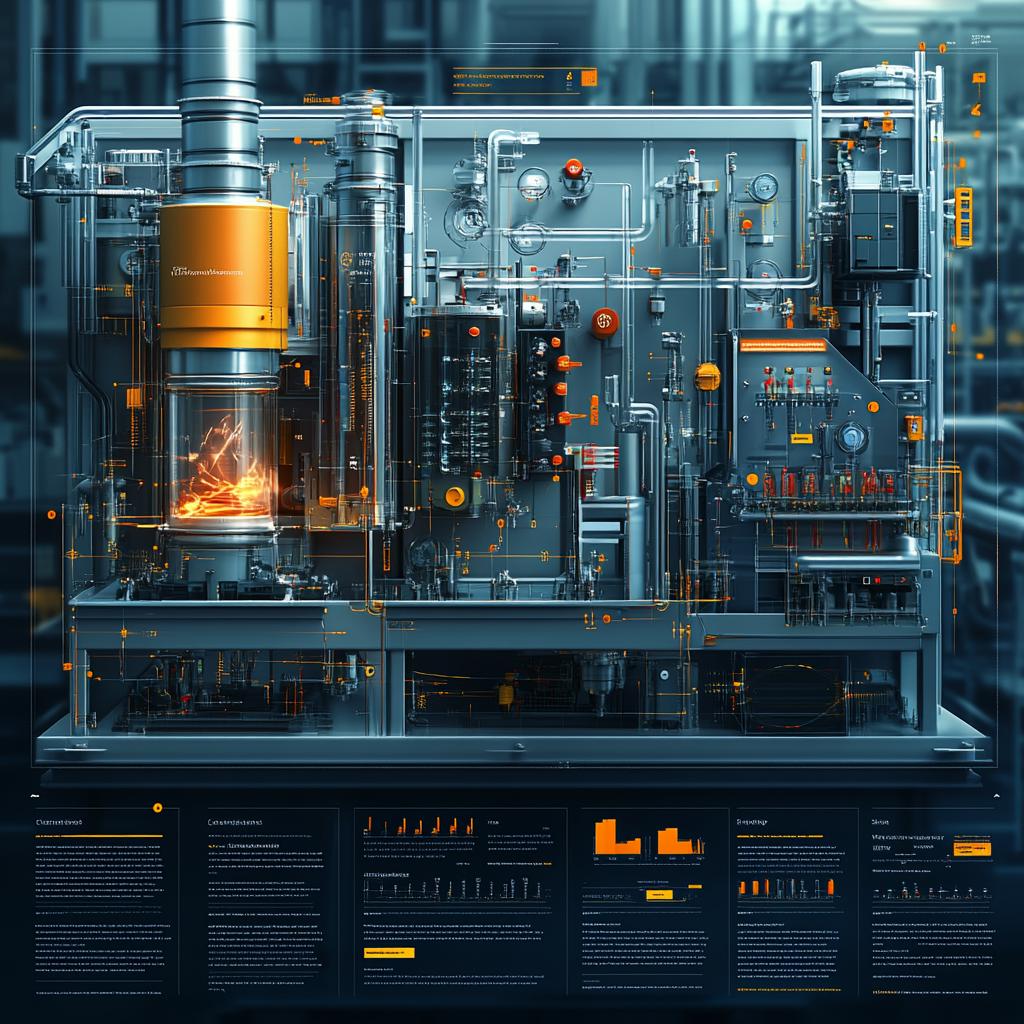
Concentration calculation:
The detector registers the reduced light intensity and transmits this information to the sensor's evaluation electronics. Here, the difference in intensity between the original light source and the light arriving at the detector is calculated. This difference is directly related to the concentration of the specific gas. By calibrating and using reference values, the sensor can calculate exactly how much of the gas is present in the sample.
Reference measurement:
To ensure accurate measurements, many NDIR sensors have a second optical path that serves as a reference channel. In this channel, infrared light is measured at a wavelength that is not absorbed by the gas to be detected. This reference channel helps to compensate for external influences such as fluctuations in light intensity or environmental conditions (e.g. changes in temperature and pressure). In this way, changes in the IR source intensity or impurities in the measuring chamber can be detected and compensated for, which further increases the precision of the measurement.
Signal processing:
The data collected on light absorption is processed by electronic circuits and converted into a concentration value. This takes into account not only the strength of the absorption, but also the speed at which the gas concentration changes. This enables a fast response time of the sensor, which is particularly important in safety-critical applications such as material testing, where fast and precise information is crucial.
NDIR technology offers numerous advantages over other measurement methods. It is non-contact, which means that the sensor is not directly affected by the gas flow and therefore has a longer life and low maintenance requirements. As NDIR technology is based on infrared absorption, it is also highly selective - it can accurately detect certain gases without being disturbed by other gases that do not absorb the same IR spectrum.
Advantages of smartGAS analyzers for material testing
The Burning Material Test is one of the most important methods in material testing to assess the flammability and safety of materials. NDIR sensors (non-dispersive infrared sensors) play a central role in this by precisely measuring the gases produced during combustion processes. These gases, including CO₂, CO and hydrocarbons, provide essential information about how a material reacts to heat and fire. One of the outstanding features of NDIR sensors is their ability to detect these gases quickly and reliably. However, not only the sensors themselves, but also the smartGAS analyzers offer decisive advantages to make material testing even more efficient and precise.
The smartGAS analyzers are characterized by their versatility. Thanks to their customizable measuring ranges, they can be used for different specific applications in materials testing. This means that depending on the type of material to be tested or the gases to be measured, the analyzers can be individually configured to achieve the best results. This makes them an indispensable tool for companies that require such flexible and accurate solutions for their materials testing.
In addition to their versatility, smartGAS analyzers also offer unparalleled accuracy. This is particularly important when it comes to assessing the safety of materials and determining whether they meet strict requirements and standards. Thanks to this conciseness, companies can be sure that their materials are reliably tested and potential risks are detected at an early stage.
smartGAS analyzers carry out their continuous data transmission at a frequency of 10 Hz. This ensures that gas concentrations can be monitored in real time throughout the entire combustion process. The seamless recording of data makes it possible to precisely track the entire test process and obtain meaningful results. Critical changes in gas behavior can therefore no longer go unnoticed thanks to constant monitoring.
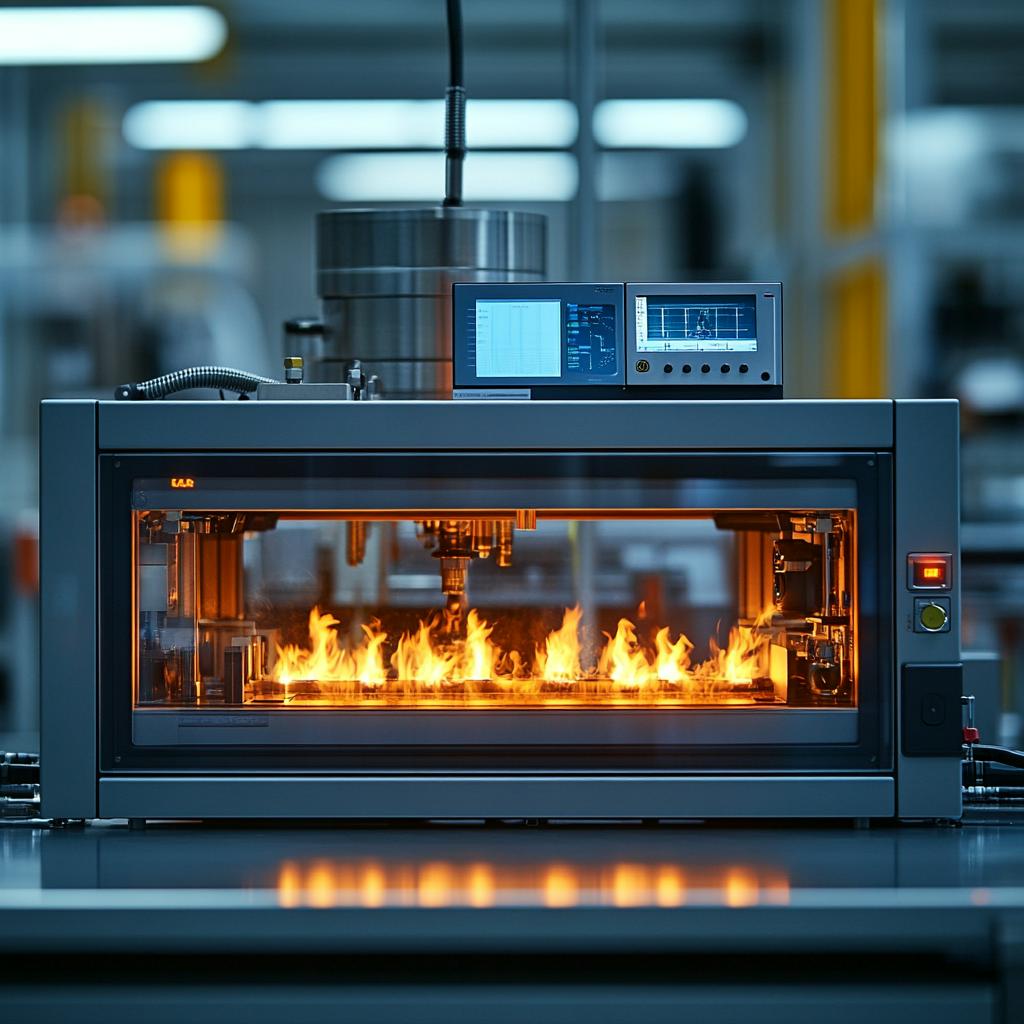
The combination of the precise NDIR sensors and the versatile smartGAS analyzers creates a powerful system for material testing. These technologies work hand in hand to deliver accurate, reliable and fast results, which are essential in safety-critical testing situations. Companies benefit from these solutions through improved testing processes that not only enhance safety but also increase efficiency.
Application spectra of NDIR sensors and analyzers
NDIR sensors are used in environmental monitoring to measure the concentrations of greenhouse gases such as CO₂ in the atmosphere. They help to monitor air quality and ensure compliance with emission limits. They also play an important role in industrial process control by monitoring the composition of process gases, thereby reducing unwanted emissions.
Another important aspect is their contribution to sustainable development. By monitoring emissions in real time, NDIR sensors help to reduce CO₂ emissions in industrial processes and thus support international climate targets. In energy generation, both from fossil and renewable sources, they help to optimize processes and minimize the ecological footprint.
Technological innovations in NDIR sensors
One of the most important innovations in material testing is the further development of NDIR sensor technology. The use of MEMS-based IR sources (Micro-Electro-Mechanical Systems) enables even more precise and efficient gas measurement. These advanced IR sources significantly improve the sensitivity and reliability of the measurements.
The smartGAS analyzers complement this technology by not only processing the collected data precisely, but also offering the flexibility that modern testing processes require. Thanks to their customizable measuring ranges, the smartGAS analyzers can be used for various applications in materials testing. Whether testing in the automotive, construction or aerospace industries, the analyzers can be tailored specifically to the task at hand, significantly increasing the efficiency of the tests.
In the future of materials testing, it will be increasingly important
to use technologies that maximize both precision and efficiency. The
NDIR sensors and smartGAS analyzers are pioneers in this field and offer
companies the opportunity to take their testing processes to a new
level. With advanced innovations such as MEMS-based IR sources and
high-precision data transmission, these systems offer everything needed
to meet future material testing requirements.
Sustainability and environmental friendliness
In materials testing, fast and reliable acquisition of measurement data is crucial, especially when it comes to safety-critical applications such as the burning material test. This is where NDIR sensors (non-dispersive infrared sensors) come into play, enabling fast and precise gas measurement. Thanks to their high sensitivity and short response time, these sensors are able to detect gases such as CO₂, CO and hydrocarbons released during the combustion process in real time. They have therefore become an indispensable technology when it comes to making quick decisions based on the data collected.
The NDIR sensors offer an extremely fast response time, with a T90 time of less than 4 seconds. This means that the sensors can detect 90 % of the final gas concentration within a very short time, which is an enormous advantage in test situations. This speed also allows users to react immediately to the measurement results. This is particularly essential when monitoring the flammability of materials in order to minimize potential risks.
In addition to their speed, NDIR sensors are also known for their high sensitivity. Even the smallest gas concentrations can be detected precisely, which enables extremely detailed and accurate analysis. This makes it possible to detect even the smallest deviations in the gas composition and draw conclusions about the safety and quality of a material.
NDIR sensors are considered to be extremely robust and durable. In test environments where high temperatures, aggressive chemical conditions or strong physical stresses prevail, the sensors retain their high performance and continue to deliver fast and precise measurement results. They are therefore ideal for use in industry, where high demands are placed on the resilience of the test equipment.
Conclusion
The Burning Material Test is a component of material testing to evaluate the flammability and fire behavior of materials. In this context, smartGAS analyzers offer solutions that significantly improve the testing process and provide more accurate results. The accurate analysis of gas concentrations makes it possible to better understand the fire hazard of a material and make informed decisions about its safety.
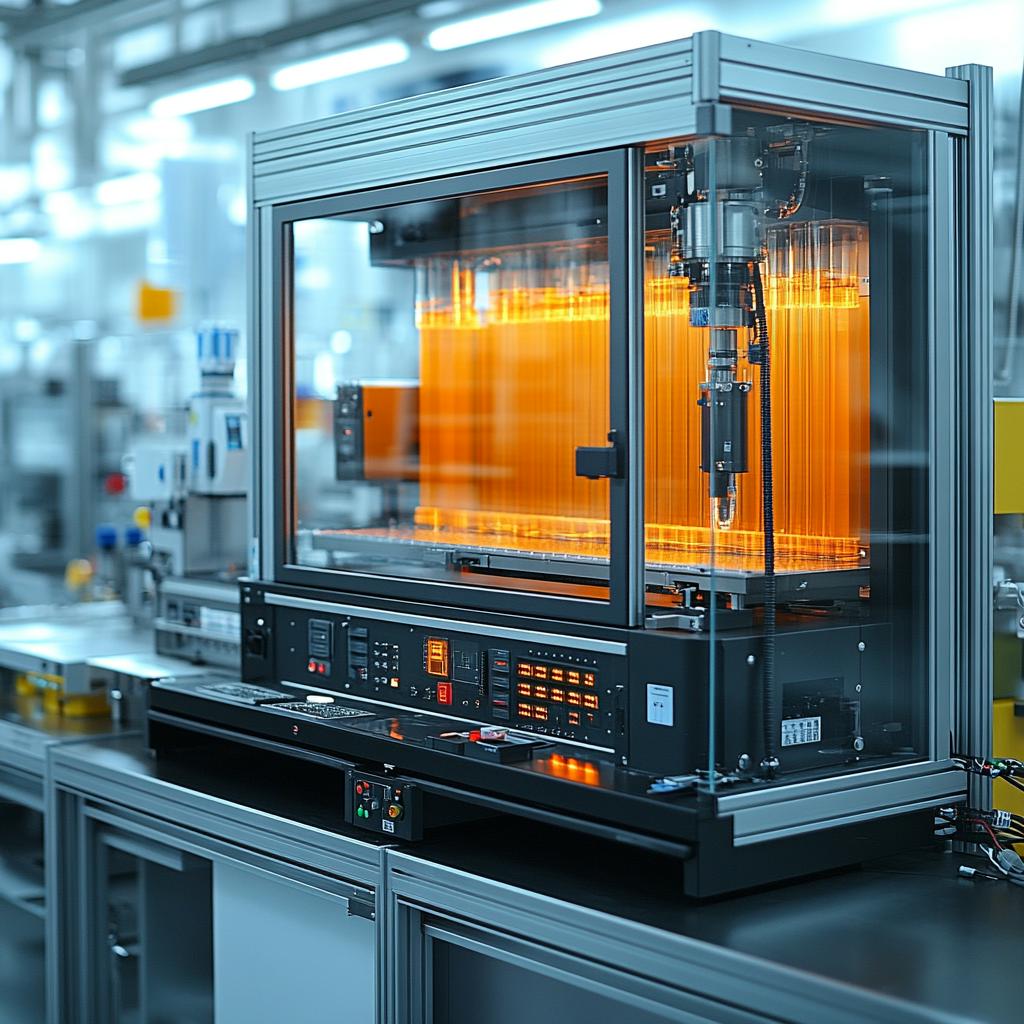
One of the main advantages of smartGAS analyzers is their extreme versatility. They offer customizable measurement ranges that can be configured for different applications and material types. This makes them a flexible solution that is ideal for various industries, from automotive to construction. Regardless of the type of material or specific testing requirements, the smartGAS analyzers can provide accurate data that enables a comprehensive evaluation of the material.
In summary, smartGAS analyzers offer a unique solution for material testing by providing precise, versatile and reliable measurements. Their adaptability and accuracy ensure that materials are evaluated to the highest safety standards. Companies using smartGAS analyzers in their testing processes benefit from more efficient, accurate and safer testing, resulting in higher quality of tested materials.